6 steps to efficient preventive maintenance
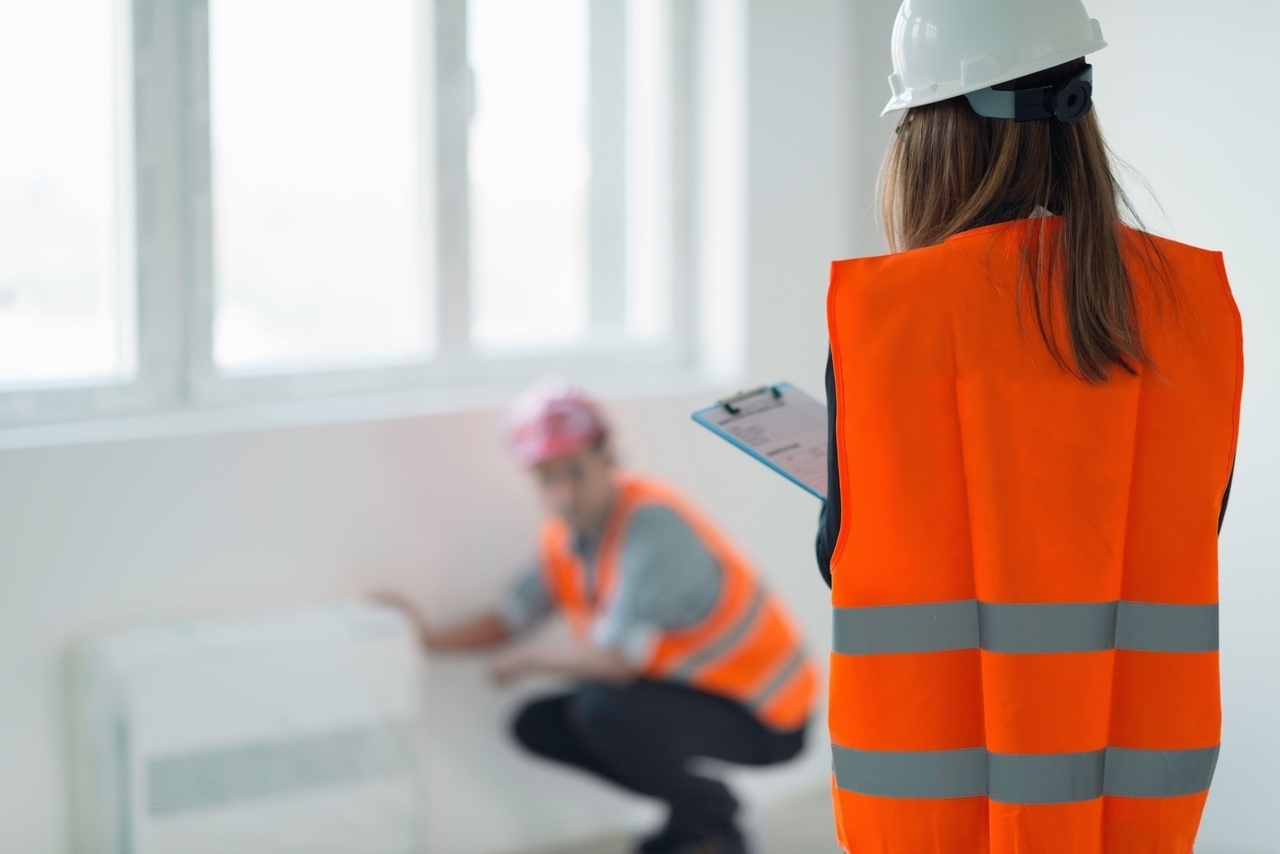
Sponsored contentÂ
The only way to develop effective types of preventive maintenance is with the help of management software. These are sophisticated tools that guide you on every route and provide a step by step breakdown of each process.
With these CMMS solutions or Computerized Maintenance Management System Solutions, one can track the entire operation back to a single point on a restricted dashboard.
Here are the six steps to having a bullet-proof preventive maintenance system for any establishment.
1. Identify Equipment.
The ideal benefit of making such a plan is the use of pre-made layouts and preventive maintenance checklists. This practice allows you to sort the equipment by location, asset-types, or inspection-needs. Once all the information about the various assets updates on the software, it becomes easier to narrow down actions.
The assets are divided by floor-location on the dashboard, allowing the maintenance manager to pick a singular task for each day. These assets can be in the form of fire-exits, a piece of equipment, electric lines, replacing parts, and much more. A comprehensive map of the floor can be used to single-out the operating condition too.Â
2. Create a Recurring PM Task
The basis of preventive maintenance is the use of a preventive maintenance schedule to ensure the machines do not run-to-damage and avoid unplanned downtime. They are steps taken to prevent the worse from occurring. This process is done by setting up a preventive maintenance plan within the software for critical assets.
Using the scheduler available, one can set up these PM tasks to a custom-repeat date. They can be daily, three times a week, the first Friday of each month, and many other variants. Based on the need for maintenance, wear of the machine, or change of parts — the person-in-charge decides the recurring plans. This routine maintenance adds to the application data-base for flaw-less fulfilment and documentation.
3. Update Documents
A computerized maintenance management system or CMMS can save all the files, for each piece of equipment, in a single palace. This collection occurs from cloud-based or hard-storage methods.
When saved on the cloud, there is no limit to the storage. This space allows the routine maintenance team to keep all records such as asset documents, maintenance costs, bills & receipts, user manual, status reports, repair-records, failure reports, commissioning reports, and much more.
Some advanced software also allows you to upload these documents into PDF format, making it easier for global access and download onto any system-type. These files can also be accessed through tags and filters, making it more comfortable for the team to track desired documents in a sea of information.
4. Review of Reports On the Dashboard.
Once you have all the steps in place, it’s time to examine the progress. This review happens in the form of reports and statistics– stats display essential information that helps gauge the health of the assets, repairs and replacements history, and other noteworthy data. This collection assists the company plans further purchase or improve existing systems.
This information is also helpful in creating annual reports, performance summaries, and management reports. They help the company-heads or floor managers determine insights about the operations and re-examine the preventive maintenance pm checklist.Â
When you use the best preventive maintenance software, the reports are also correctly generated and organized within the dashboard. This means the admin can extract the information based on filters like user-name, equipment failure, asset-category, and more. One does not need to build reports from scratch; let the computer do it faster and free-of-errors.
5. Provide Remote Access.Â
A significant advantage of using a facility management software is the ability to share all the data, and the progress, with the whole team using a single point-of-access. Using an election device, the entire team can access maintenance details, give remarks on schedules, and add receipts or reports.
Workers are no longer chained to a bench or a desktop computer to finish the preventive maintenance tasks. The dashboard is accessible from tablets, phones, and laptops. It’s as simple as downloading any application form the mobile-application-store.Â
It also reduced the need to take prints, share files, and maintain room-full of records. They will also prevent duplication of documents since all users will access only a single page. Some advanced CMMS software also comes with communication channels that allow you to share real-time information with individuals or work order groups.  Â
6. Audit Trails.
Once you plan and execute a maintenance strategy, some companies have auditing teams that study the workflow and ensure the tasks are up-to quality standards. They also determine if the preventive maintenance tasks are done on time and with the right steps. Here the computer-maintenance schedule comes in handy. This can also be used to coordinate reactive maintenance and predictive maintenance strategies.
The admin can find every action on each asset in a perfect record. They are time-stamped and very hard to manipulate. This step allows the managers to keep the team on track and reassure each person’s accountability.
Final Thoughts
Facility management software provides efficiency and productivity to a whole team, at minimal costs. Since they can also be used to communicate and store data, they give an additional CMR and Cloud-Storage utility.
In this world of modern technology; modernized solutions and problem-solving methods are the inevitable way to stay ahead of the curve.